

NOISE & VIBRATION MONITORING
Measurement of Workplace Noise
The Control of Noise at Work Regulations 2005
Do you have equipment that is fixed or portable that required noise survey carried out to determine if the noise exceeds the permissible limits, Or do you have staff who could be subjected to loud continual noise pollution?
Health and Safety Services can carry out your annual noise survey or assess equipment that you are not sure of. In many cases when you are purchasing new equipment your procurement officer or company advisor should ask for the Safety Data Sheets (SDS) all of the information relating to your equipment will be in the datasheets, if you have older equipment then this can be an issue to find specifications on that equipment.
Health and Safety Services using the latest equipment can carry out a Noise Assessment of your workplace and running equipment. By carrying out the noise survey you will be compiling to The Control of Noise at Work Regulations 2005
Noise Assessment Method
The aim of a noise assessment is to help you decide what you need to do to make sure the health and safety of your employees who are exposed to noise. It is more than just taking measurements of noise. Sometimes measurements may not even be necessary. Please refer to the HSE guidance on noise assessment for more information.
-
Identify where there may be a risk from noise and who is likely to be affected e.g. use of Task Analysis.
-
Turn on and setup the noise meter (consider weighting, range, fast/slow).
-
Measure (if required) the noise output at set locations determined by a competent person, e.g. where operators are sitting or standing, consider their different tasks at different times of the day including a background reading.
-
Operate at arm’s length, but in a position, you can read the screen easily, as reflections from the body can cause reading errors.
-
Record a 30 second reading using a timer (you may need to do this throughout the day).
-
Record the Leq (dB(A)).
-
Record the dB(C) peak value.
-
To record a dB(SIL) cycle through the recording until you reach 500Hz, 1.00K, 2.00K and 4.00K in the Hz location, recording the dB value at each, then take an average.
-
Calculate a reliable estimate of your employees’ exposures, and compare the exposure with the exposure action values and limit values (see below).
-
Identify what you need to do to comply with the law, e.g. whether noise-control measures or hearing protection are needed, and, if so, where and what type.
-
Identify any employees who need to be provided with health surveillance and whether any are at particular risk.
-
Record the findings of your risk / noise assessment.
-
Review your risk / noise assessment regularly (I suggest yearly) or if circumstances in your workplace change and affect noise exposures.

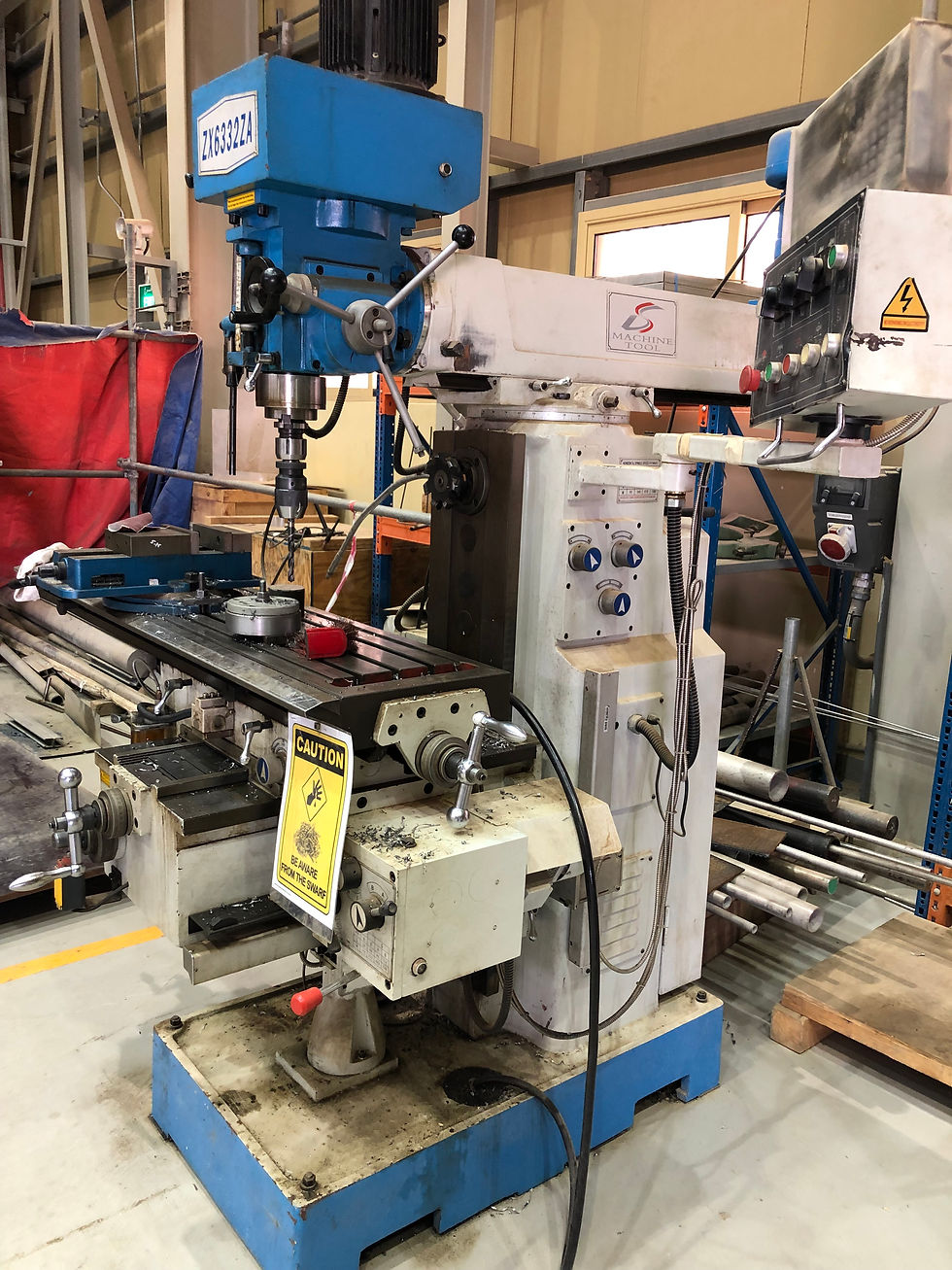

Noise Limits
UK Health and Safety Executive (HSE) Control of Noise at Work Regulations (2005) have been put in place to protect employees from noise. The Noise Regulations define ‘exposure action values. Levels of noise exposure which, if exceeded, require the employer to take mitigating actions. Once a noise assessment has been conducted, compare your noise exposure with the action values to know what actions are required to reduce noise exposure to as low as reasonably practicable (see HSE guidance on noise).
You are required to make a reliable, representative estimate of a workers’ daily personal noise exposure. Daily personal noise exposure, or LEP,d, represents a daily noise ‘dose’. A combination of ‘how loud’ and ‘how long exposed’ for the various noises that a person is exposed to in a working day.
Hand Arm Vibration HAV’s Assessments
Health and Safety Services will carryout your hand arm vibration assessments using the latest equipment. The team are fully trained and understand the needs of our clients.
When we talk about HAV’s and how to manage them in the work place! most times, we will just review your current procedures and how you track the health of your staff as in many cases we have found that this was all that was required. Health and Safety Services will review your current Risk Assessments and where necessary produce new risk assessments.
As a company you will be aware of the Regulations relating to Vibration and the effects that it could have on the long-term health of the staff (most common; vibration white finger).
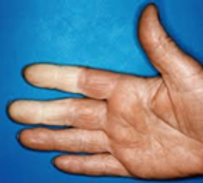
To meet the legal requirements, you may only require a simple guideline updating or full equipment evaluation. At Health and Safety Services we meet your requirements and not hard sell full inspections.
Regular exposure to vibrations can lead to a number of debilitating conditions; the two most common are Hand-Arm Vibration Syndrome (HAVS) and Carpal Tunnel Syndrome (CTS).
Both conditions can cause numbness, weakness, pain, and, if left untreated, loss of control in a person’s hands; it’s important that you’re able to recognise the early warning signs and know when your exposure exceeds safe limits so you can act before the damage becomes permanent.
Both you and your employer have a responsibility to make sure that you’re safe at work. Your employer is responsible for monitoring and limiting your exposure to vibrations, for making sure that you’re properly trained and have all the information you need to stay safe, and for providing protective equipment. You have a duty to follow their safety instructions and to properly use/ wear any safety equipment they provide. Understand your responsibilities as an employee or employer and avoid HAVS with our Hand/Arm Vibration Awareness Training.

Practical Advice
Hand-Arm Vibration Management Programme – Best Practice Guide
The following is a step-by-step check list of the components of any effective HAV risk management programme that should be included in any risk assessment report. Contact us for more on any of the element(s) for which you need more information.
1.
Create a vibrating tool / plant register: this always takes much longer and turns up many more tools than you expect. Make sure you have sufficient information to define a tool and an operation – “blue drill” is not sufficient! As a minimum, you need make, model, accessory, the operation for which it is used and the material (metal, plastic, grass, scrub etc).
2.
Carry out a HAV risk assessment – don’t measure unless you absolutely must. Surely everyone has already done this? The key message from the HSE is: “Don’t measure vibration unless you absolutely must”.
3.
Implement an effective HAV risk management programme: this includes operational factors, working conditions, behaviour, ergonomics, symptom reporting systems etc. Note that this does not include PPE as there is no effective PPE for hand-arm vibration – although you might not get that impression from reading the technical literature from various suppliers.
4.
Reduce the levels of vibration via tool maintenance and vibration control measures: evaluate the sensitivity of tool and plant vibration to their mechanical condition so that maintenance can be prioritised. The level of vibration from tools can range from completely unaffected to very sensitive to tool condition. In some cases, retro-fit engineering modifications can substantially reduce vibration in some cases.
5.
Hire / Buy low vibration tools and plant: base your decision on field vibration data. Include operational, productivity and ergonomic factors as well as levels of hand-arm vibration in your selection criteria. Be aware, however, that the commonly used HAV data traffic light system based on manufacturers’ data often seriously underestimates the risks.
6.
Training: as operator risk can be very dependent on behaviour, training is a very important risk management element – toolbox talks, management briefings and full HAV competency as appropriate.
7.
Health Surveillance: introduce a health surveillance programme for all workers who are likely to be exposed above the current Exposure Action Value (A(8) of 2.5 m/s^2). This includes education, reporting system, health checks and communication.
8.
Audit the risk management programme: check that you are implementing current best practice for all of the above elements – in practice and not just on paper. We have often found that the audit will turn up disconnects between theory and practice and that risk management can be improved in parallel with significant cost savings.
Optimising Vibrating Tool Maintenance Systems – HAV tool condition, testing and maintenance pitfalls…
How to focus your maintenance on the right tools
The costs associated with managing the risks from Hand-Arm Vibration can be reduced very substantially by introducing an effective condition-based maintenance programme. We have collated the field vibration values for thousands of tools to generate statistics that show how maintenance affects vibration. For example, for standard breakers or rivet guns, the vibration from an “as new” tool is little different from an old, worn tool. In contrast, a poorly maintained angle grinder or leaf blower will generate several times the vibration of a well-maintained unit as shown in this graphic of the statistical spread of vibration levels. It shows that as the vibration from rivet guns changes very little with condition, maintenance is not important with respect to reducing the risk of HAVS.
This information can be used to improve your tool maintenance programme by concentrating resources only on those tools that pose the greatest risk if they are not well maintained. Contact us if you like to discuss the options to optimise your tool maintenance programme.
Optimising vibrating tool maintenance contracts – beware maintenance contract HAV meter measurements
Increasingly, post-maintenance vibration checks are included in tool maintenance contracts. Unfortunately, as they are usually carried out under no load using a HAV meter, this provides no useful information about tool condition. HAV meter measurements cannot be compared with the manufacturers’ (ISO 28927) declared values as the test conditions are completely different, nor do they provide any useful information about the mechanical condition of the tool (except gross issues that are obvious). They could be used to provide risk assessment values, but only if the tool is tested under simulated conditions that accurately reflect those in the final workplace.
HAV meter measurements do not detect most tool faults as they filter out much of the vibration associated with component and assembly faults. Consequently, a newly fitted damaged bearing will not be detected – despite the fact that it will quickly lead to much higher levels of operator HAV exposure in normal tool use.
The only way to evaluate HAV tool condition accurately is to use the HAV-Test tool vibration signature analysis system. This takes a few seconds to assess the mechanical condition of tools pre-overhaul. As around 50% of tools are typically in perfect condition, they need not be overhauled, cutting maintenance costs and increasing tool availability. A post-overhaul test ensures that the maintenance procedure has returned each tool to “as new” condition within the manufacturers’ specification. This corresponds to the lowest vibration – and lowest HAV risk – possible for each tool.
HAV Management Audit – dramatically reduce HAV risk management costs
The Audit is the fastest and most effective way to ensure compliance with current best practice in HAV assessment and risk management. It benchmarks your policy and procedures and generates a detailed Action Plan with full technical support based on innovations that can reduce costs by up to 80%.
The Health and Safety Executive has produced free information that you can use in conjunction with Information from; Manufacturers guidelines, Vibration monitoring equipment.
General Information
Pedestal Grinding
Flash removal from hand-held aluminium components generated 32m/s^2 – the Exposure Limit Value (ELV) would be reached in 12 minutes, severely limiting production. Detailed analysis revealed dominant vibration was caused by a pedestal grinder component rest resonance. It was replaced by a floor mounted version that improved the ergonomics and reduced the vibration to 1m/s^2, allowing unlimited use without risk of HAVs.
Concrete Ramming Tool
A hand-held Ingersol Rand sand rammer packing concrete lintel moulds generated 28m/s^2 with a maximum trigger time of only 15 minutes/day before reaching the Exposure Limit Value, seriously limiting production. We designed a mass / sprung balance system that reduced the vibration to 11.5m/s^2, extending the “safe” trigger time to 90 minutes/day. Combined with substantial ergonomic improvements, operator HAVS risk was virtually eliminated and there were large productivity gains. As the whole project was completed within days (no site visit) via information (data, video) forwarded by email, the total cost was a few £hundred, making it self-financing over a few days.
Riveting Aluminium Panels
Vibration from riveting on a bench jig posed a very high risk of HAVS. Our redesigned, stiffer jig reduced the riveting time by 50% and the vibration by 25%. This cut the overall operator dose by nearly 90% – improving productivity as a side effect.
Impact Wrench Bolt Tightening
The operator used a spanner on one side of conveyor frames and an impact wrench on the other, producing significant HAVS risk in both hands. We recommended a larger, more ergonomic spanner and a more powerful wrench. These measures halved the vibration dose and significantly improved productivity.
Die Grinders
High-speed bits were used to trim aluminium panels, but the tool speed was far too low. Changing the die grinder for a high-speed unit to match the bit left the vibration unchanged, but the improved efficiency cut working time from 20 minutes to 2 minutes, reducing the risk by factor of three. On a similar operation, simply ensuring the grinding bit was pushed fully into the chuck up reduced the level of vibration by a factor of x4.